Additive Manufacturing
Additive Manufacturing serving power generation.
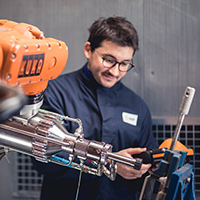
Supplying quality components within firm deadlines is a major challenge for the maintenance and availability of EDF's power plants. Additive manufacturing is a growing industry trend that has the potential to revolutionise the design, repair and supply chain of components for both new build and existing facilities.
Project developed by the EDF group in partnership with CEA (French Alternative Energies and Atomic Energy Commission), Framatome, Naval Groupe, AFH (Additive Factory Hub), Team Henry Fabre, Institut de Soudure, Cirtes, Rosatom, CNNC, etc.
Additive manufacturing consists of making or repairing parts by adding material, layer by layer, from a digital file.
EDF's R&D is conducting a process evaluation to understand the contribution of these new methods to the Group's activities. Main goal: to demonstrate the ability of 3D printing to produce quality components that meet the service life and safety requirements for EDF's power generation fleet.
The Kapl'EAU 3D project is an example of 3D printing applied to the hydroelectric power generation facilities. 3D printing makes it possible to create replicas with the properties of the maintenance spare parts, which can then meet the same visual and technical specifications as the original parts, for both conditions of use and durability.
The project uses the polymer thread deposition method or wire arc deposition (WAAM), depending on the needs of the parts. The 3D printer can therefore shape a hydroelectric blade or a clamp or even weld. The technology is highly compatible with the needs of the hydroelectric industry and the standards of the sector.